Luyten 3D achieves main milestone in development expertise
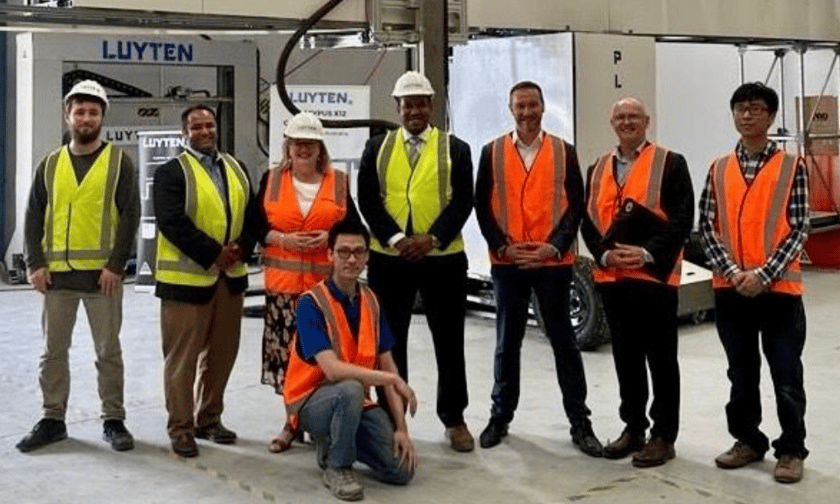
Australian 3D printing firm Luyten 3D has accomplished a big achievement by establishing the primary 3D-printed two-storey constructing within the southern hemisphere.
The 2-storey granny flat was printed in simply 32 hours at Luyten 3D’s world headquarters in Melbourne, utilizing their superior Platypus X12 cell 3D printer (pictured above).
Modern expertise and development
Luyten 3D, identified for its efforts in 3D development expertise, used the Platypus X12 printer, the biggest cell AI-powered 3D printer globally, to print the constructing. The Platypus X12 can increase to 6 meters in peak and 12 meters in size, and it operates utilizing a self-propelled crane, making it extremely adaptable for various development websites.
EMBED LINK: <iframe width=”560″ peak=”315″ src=”https://www.youtube.com/embed/4ebp33K0Wg8?si=x9rht3VPO4fJBZCC” title=”YouTube video participant” frameborder=”0″ permit=”accelerometer; autoplay; clipboard-write; encrypted-media; gyroscope; picture-in-picture; web-share” referrerpolicy=”strict-origin-when-cross-origin” allowfullscreen></iframe>
“We’re extraordinarily proud to grow to be the primary ever 3D printing firm within the constructing and development sector to ship on such a monumental achievement,” mentioned Ahmed Mahil, founder, CEO and world president of Luyten 3D.
Environment friendly and cost-effective development
The 2-storey granny flat, comprising two bedrooms, a kitchen, lavatory, and residing space, was printed in a single steady session by two employees members over two and a half days. This development technique considerably reduces construct time and prices, in comparison with conventional constructing strategies.
“Via our telescopically transformative Platypus X12 printer, we’ve got made it doable for this printing to occur seamlessly in a single printing session with out the necessity for the involvement of another heavy equipment,” Mahil mentioned.
Sustainable and high-performance supplies
Luyten 3D used their proprietary concrete combine, Ultimatecrete Ultraeco, to print the constructing. This combine makes use of 20% much less cement than the unique eco-friendly Ultimatecrete, enhancing sustainability whereas sustaining excessive efficiency.
Addressing housing challenges
Mahil emphasised the potential of 3D printing to handle housing affordability and development effectivity.
“3D printing considerably reduces construct time and cuts prices for the creation of the structural framework,” he mentioned. “Relatively than laying bricks and constructing partitions, 3D printing merely prints the construction in order that trades can then set up the ultimate components.”
The venture demonstrates the flexibility and potential of 3D printing expertise for a variety of development functions, particularly in distant or difficult places. The Platypus X12 can create sturdy, weather-resistant buildings rapidly and effectively.
Way forward for development
Luyten’s 3D printing expertise allows vital reductions in waste, manufacturing time, and labour prices, the corporate mentioned.
“Conventional constructing strategies are proving too pricey for an business that has operated on mounted price contracts and archaic constructing practices,” Mahil mentioned. “3D printing isn’t only for primary buildings. As we’ve got proven, 3D printing is able to delivering a broad vary of properties for various and difficult places.”
Get the most well liked and freshest mortgage information delivered proper into your inbox. Subscribe now to our FREE every day publication.
Associated Tales
Sustain with the newest information and occasions
Be part of our mailing record, it’s free!
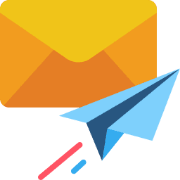